Process & Safety
systematic analysis of all relevant production processes
The safety of engineering processes
The department of process safety deals with the safety of engineering processes. The service ranges from the testing of individual substances to safety studies for specific chemical processes or the systematic analysis of all relevant production processes of an enterprise up to the failure analysis after occurred events.
There is no ZERO-RISK ...
The right dosage is crucial! enrichments, impurities, delayed or non-onset reaction processes or failure of the cooling – these are also dangers that can convert a previously safe chemical reaction into an uncontrolled state.
Everyone knows from their own experience: There is no zero risk. It is therefore important to use chemical expertise and experience to make chemical processes as safe as possible.
Inherently safe processes!
The Process Safety department is working intensively on the implementation of the motto “Avoiding dangers by developing inherently safe processes”. If, after a detailed safety assessment, an unacceptable residual risk remains, additional measures are taken. In this case, our consultants recommend suitable protection systems and state-of-the-art technology. If technical measures are not possible, inadequate or disproportionate, the necessary security will be achieved through complementary organizational concepts.
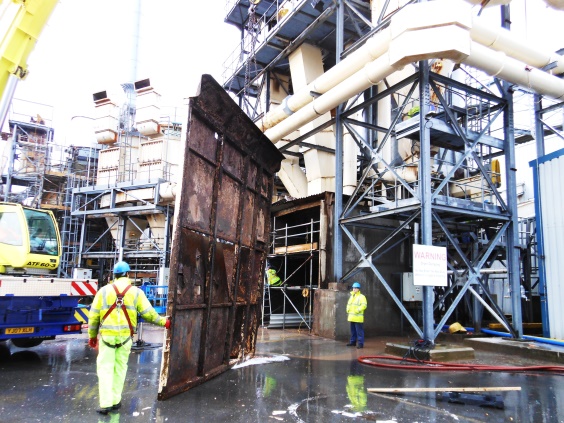
Technical Process Safety
Our process industry services cover technical safety and are wide ranging; from chemical syntheses where the hazard may arise from uncontrolled exothermic reaction, gaseous emissions or the use of solvents, to solids handling operations involving explosible (flammable) airborne powders e.g. wood, waste, cereal crops, chemical products and intermediates, etc. Post event, we offer incident investigation services, working along side regulatory authorities and legal professionals.

Assessment procedure:
Chemical Reaction Hazard (CRH) Evaluation
Exothermic runaway reactions can lead to an environmental release of toxic and/or flammable material and often are compounded by severe secondary hazards – the devastation which followed the Bophal catastrophe (1984) is without doubt one of the most publicised.
The consequences of violent exothermic runaway reaction can be just as severe as those from ignition and explosion of fuel/air mixtures. Chemical hazards principally arise from:
- Thermal instability of reactant mixtures and products
- Rapid exothermic reactions which can raise the temperature to a level which initiates decomposition or violent boiling
- Rapid gas evolution which may pressurise and rupture plant.
The effect of scale-up is particularly important. A reaction, which is apparently innocuous on the laboratory or even semi-technical scale can be disastrous on the manufacturing scale. Whereas the heat release from a highly exothermic process (e.g. catalysed polymerisation) may be controlled easily in laboratory glassware, if the same reaction is carried out in large scale plant (with a much lower surface area/vessel volume ratio), efficient cooling must be provided or a runaway reaction and over-pressurisation may occur.
The table below shows the difference in behavior between a laboratory test and a large scale reactor.
Lab Scale 100ml | Plant Scale 2.5 m3 | |
Heat loss | 3.68 W.kg-1.K-1 | 0.054 W.kg-1.K-1 |
Reaction temp 80 ⁰C | ||
Rate of heat loss | 210 ⁰C.hr-1 | 2.8 ⁰C.hr-1 |
Rate of heat production | 100 ⁰C.hr-1 | 100 ⁰C.hr-1 |
Needs Heating | Needs Cooling |
Calorimetry should consider not only the normal process but expected deviations also, For example
- Loss of agitation – is there a build up of reactants?
- Temperature/pressure deviations
- Reactant charging errors - omissions/over-charging/wrong order
- Extended reaction times
Even small scale testing (Dewar Calorimeter inside Oven) can be ‘hazardous’
Chemical reaction hazards must be considered when assessing whether a particular process can be operated safely at both pilot plant and manufacturing scales. To this end, Inburex offer a comprehensive calorimetry testing service.
Operational Hazard Assessment
Operational hazards involve fuel-air deflagrations from gases, vapours, mists/sprays and airbourne powders. In enclosed situations, explosion pressures of 7 – 10 bar.g can arise, with the potential to cause over-pressurisation and loss of containment; sometimes with devastating consequences.
The newspaper article opposite refers to a series of explosions which ripped through a city. It was not a ‘gas’ explosion – n-Hexane solvent (a water immiscible hydrocarbon with a low flash point) found its way in to storm drains. The immiscible liquid could travel for miles on the surface of the water, forming an extensive flammable atmosphere throughout the drainage system. Ignition resulted in major casualties.
A knowledge of the flammability, physical and chemical characteristics of the range of substances being handled is key to understanding the potential ignition and explosion hazards. DSEAR / ATEX and regulations worldwide aim to prevent such incidents by adopting assessment procedures which, for example:
- Systematically interrogate the plant and its procedures (HAZOP Study)
- List the hazardous properties of materials (MSDS’s)
- Prescribe inerting or ventilation requirements for mitigation
- Evaluate potential sources of ignition & control measures e.g. earthing, T ratings, etc.
- Document the findings, formally implementing the necessary safety measures and ensuring that they cannot be by-passed or undermined (see photo)
- Training is integral to this strategy.
In ALL cases, a secure Basis of safety must be clearly defined. To this end, the interplay of products, processes, systems and operating modes must be analysed in order to develop a comprehensive prevention and/or protection concept. Our experts not only apply these concepts, many have helped in their development, through Standards Organisations.
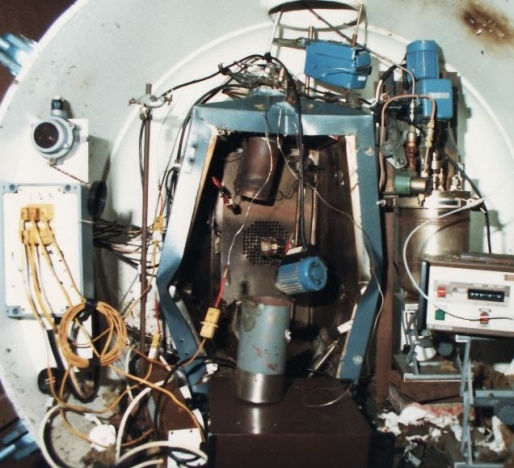
Dewar Calorimeter
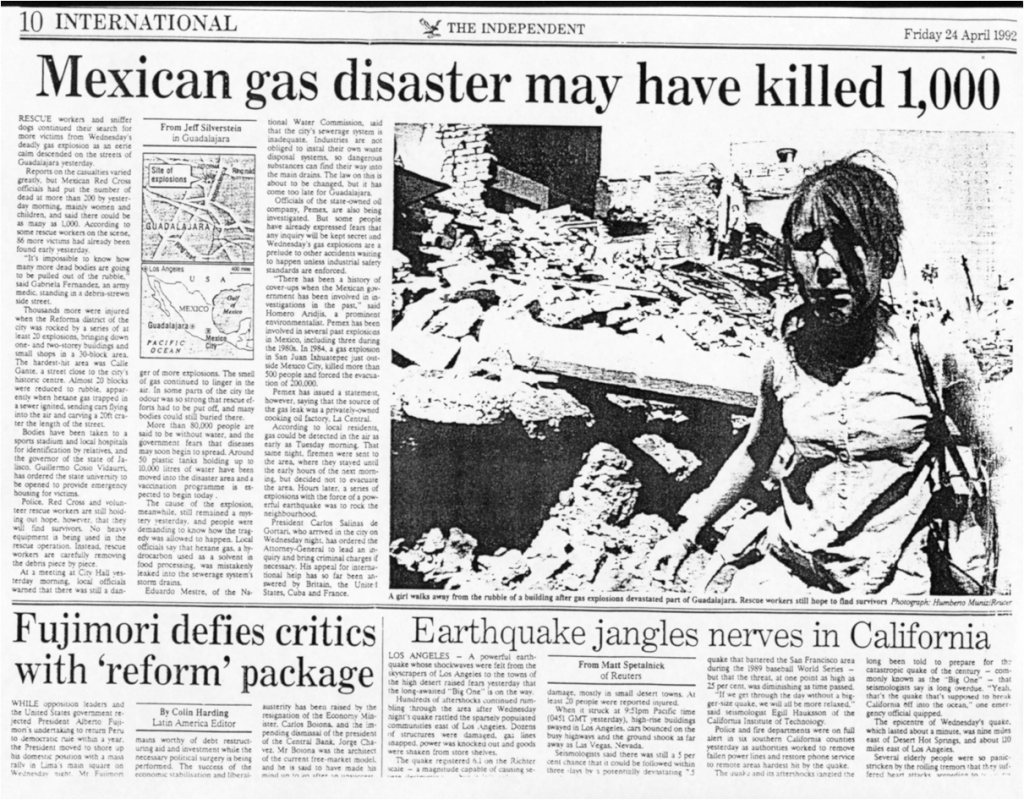
